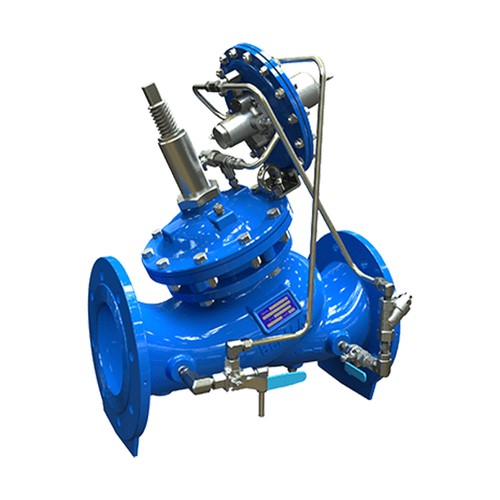
Brand: | Bermad |
Category: | Control Valves, 700 Series |
Size Range: | 50-600mm |
Connection: | EN: 50-400mm - Flanged ES: 65-600mm - Flanged |
Engineering Data: |
Product Description
The Model 790-M Burst Control Valve is a hydraulically operated, diaphragm-actuated control valve that upon sensing flow in excess of setting shuts off and locks drip tight until it is manually reset. As long as the flow is lower than the setting, the valve remains fully open, minimizing head loss.
- Zone shut off at burst
- “Older” burst susceptible networks
- Outlets from the reservoir at earthquake risk
- Vulnerable network infrastructure facilities
- Networks at risk of mechanical damage
Features and Benefits
- Line pressure driven – Independent operation
- Mechanical flow stem
- Field adjustable
- No moving parts
- No electronic components
- Highly sensitive hydraulic pilot
- Requires minimal valve-ΔP
- Tight setting window
- In-line serviceable – Easy maintenance
- Double chamber
- Moderated valve reaction
- Protected diaphragm
- No spring - Full opening
- Flexible design – Easy addition of features
- "Y" or angle, wide-body – Minimized pressure loss
- Obstacle-free, full bore – Uncompromising reliability
Major Additional Features
- Closing at pressure drop – 790-91
- Pressure reducing – 792-U
- Solenoid control – 790-55-M
- Electric override – 790-59-M
Typical Applications
Burst Control Valves in a Network
Every water system is vulnerable to bursts, whether due to system problems or external mechanical damage. This illustration shows a reservoir feeding a downhill line with lower-elevation consumers.
In case of a burst, each Model 790-M protects against flooding lower elevation consumers. The Model 790-M, installed at the reservoir outlet, also protects against reservoir emptying.
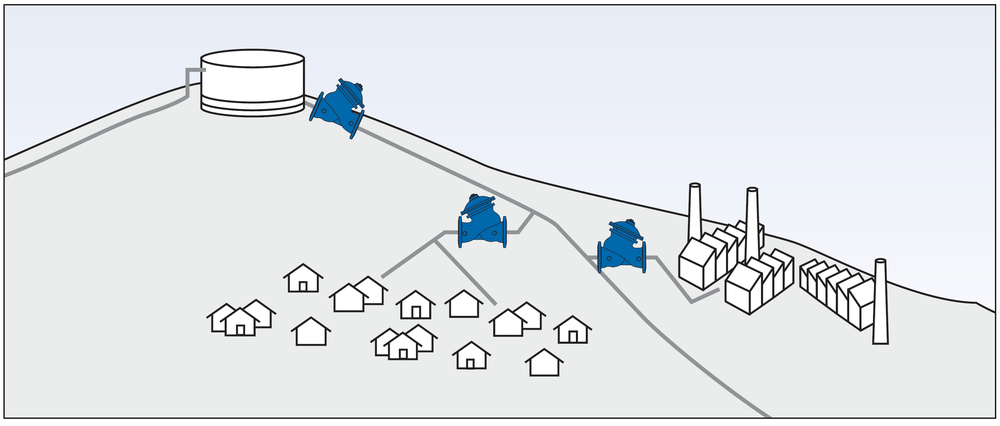
Bermad - Model 790 - Typical Application
Typical Installation
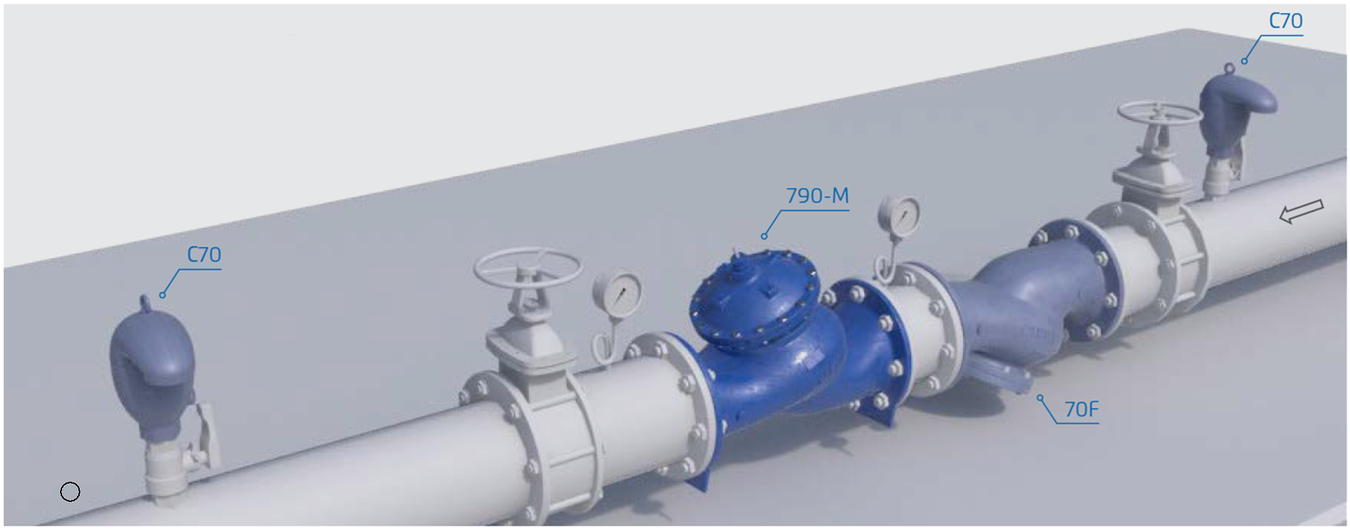
The minimum pressure required to ensure proper valve functioning is 1 bar. Where
pressure is lower, consult Deeco.
Technical Data
Operation
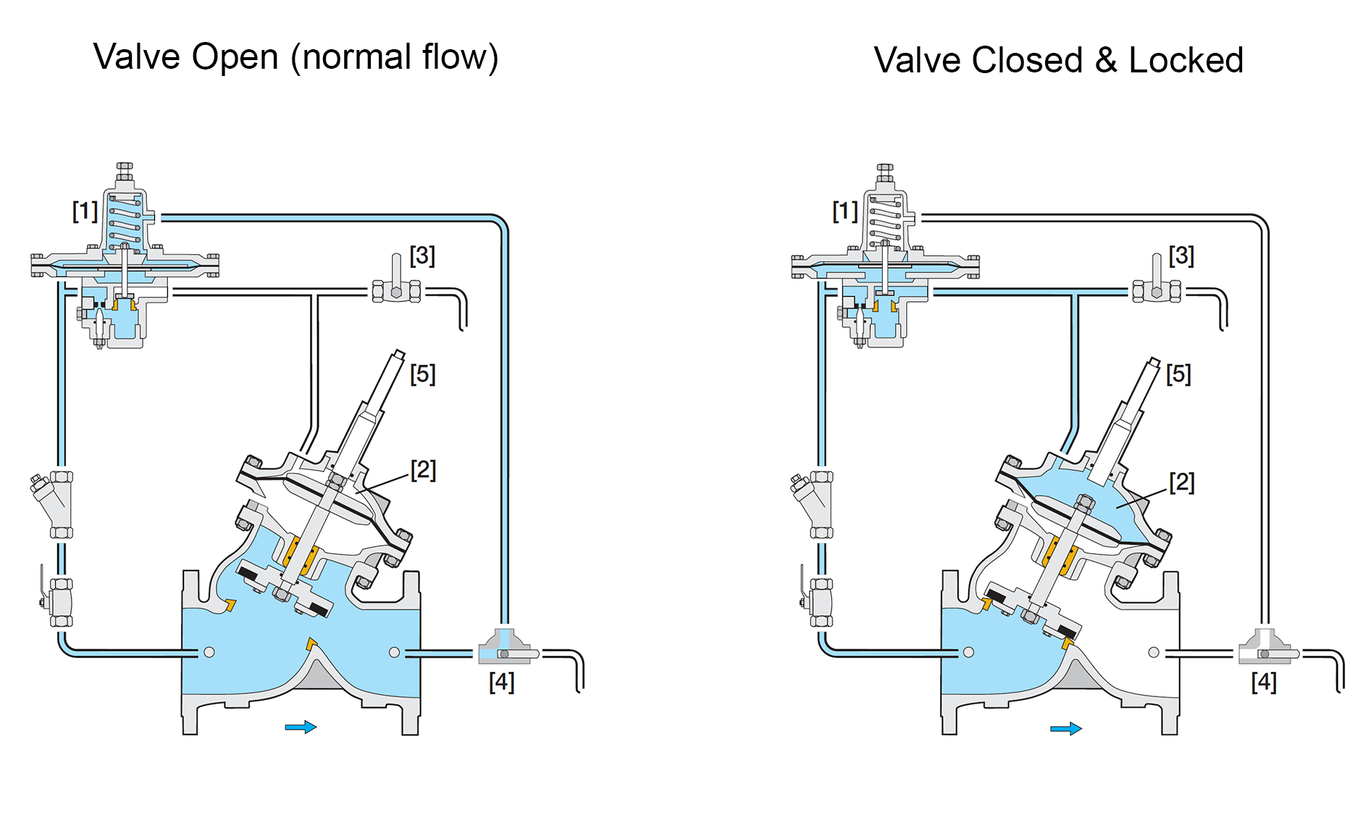
The Model 790-M is a pilot-controlled valve equipped with an adjustable, 2-Way, high sensitivity, differential pressure sustaining pilot.
The pilot [1], senses valve differential pressure. Should that pressure rise above pilot setting, the pilot opens, introducing upstream pressure into the upper control chamber [2], causing the main valve to begin an irreversible “close & lock” process.
Opening and resetting the main valve requires manual intervention by means of the manual reset valve [3]. When the differential pressure is below the pilot setting, the pilot blocks upstream pressure from the control chamber, and the main valve remains fully open. The manual test valve [4] enables the simulation of burst conditions and valve response. After testing, a reset procedure is required.
The mechanical flow stem [5] enables adjusting the closing point, to meet various flow regimes.
Engineer Specifications
Upon sensing flow in excess of setting, the Burst Control Valve shall shut off and lock drip tight until it is manually reset. As long as the flow is lower than the setting, the valve shall remain fully open, minimizing head loss.
Main Valve: The main valve shall be a center-guided, diaphragm-actuated globe valve of either oblique (Y) or angle pattern design. The body shall have a replaceable, raised, stainless steel seat ring. The valve shall have an unobstructed flow path without stem guides, bearings, or supporting ribs. The body and cover shall be ductile iron. All external bolts, nuts, and studs shall be Duplex® coated. All valve components shall be accessible and serviceable without removing the valve from the pipeline.
Actuator: The actuator assembly shall be double-chambered with an inherent separating partition between the lower surface of the diaphragm and the main valve. The actuator assembly shall not contain any closing spring or spring-like device. The entire actuator assembly (seal disk to top cover) shall be removable from the valve as an integral unit. The stainless steel valve shaft shall be center guided by a bearing in the separating partition. The replaceable radial seal disk shall include a resilient seal and shall be capable of accepting a V-Port Throttling Plug by bolting.
Control System: The control system shall consist of a 2-Way adjustable, direct acting, differential pressure sustaining pilot valve, a mechanical flow stem, cock valves, and a filter. All fittings shall be forged brass or stainless steel. The assembled valve shall be hydraulically tested and factory-adjusted to customer requirements.
Quality Assurance: The valve manufacturer shall be certified according to the ISO 9001 Quality Assurance Standard. The main valve shall be certified as a complete drinking water valve according to NSF, WRAS, and other recognized standards.
Main Valve
Valve Patterns: “Y” (globe) & angle
Size Range: 50-600mm
End Connections:
EN: 50-400mm - Flanged
ES: 65-600mm - Flanged
Others: Available on request
Working Temperature:
Water up to 60°C
Standard Materials:
Body & Actuator: Ductile Iron
Internals: Stainless Steel, Bronze & coated Steel
Diaphragm: NBR Nylon fabric-reinforced
Seals: NBR
Coating: Fusion Bonded Epoxy, RAL 5005 (Blue)
NSF & WRAS approved or Electrostatic
Polyester Powder, RAL 6017 (Green)
Control System
Standard Materials:
Accessories: Bronze, Brass, Stainless Steel & NBR
Tubing: Copper or Stainless Steel
Fittings: Forged Brass or Stainless Steel
Pilot Standard Materials:
Body: Brass, Bronze or Stainless Steel
Diaphragm covers: Fusion-bonded epoxy
coated steel
Elastomers: NBR
Springs: Stainless Steel
Internals: Stainless Steel
Pilot Valve Selection
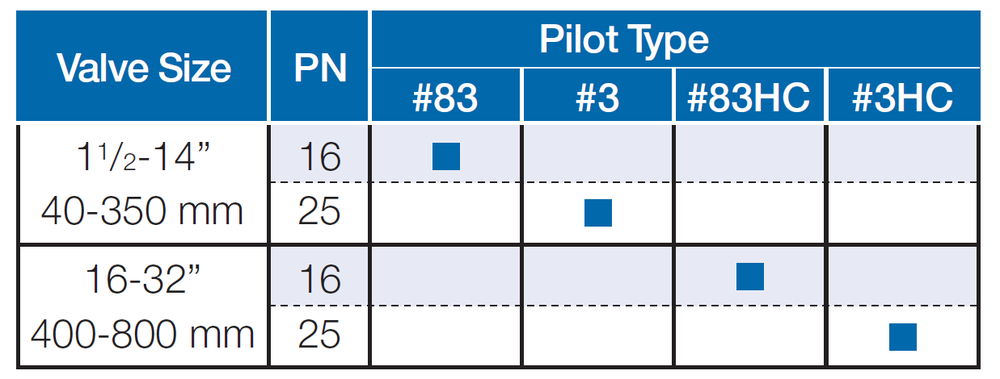
-Pilots are modified to: differential remote sensing-model “DR”.
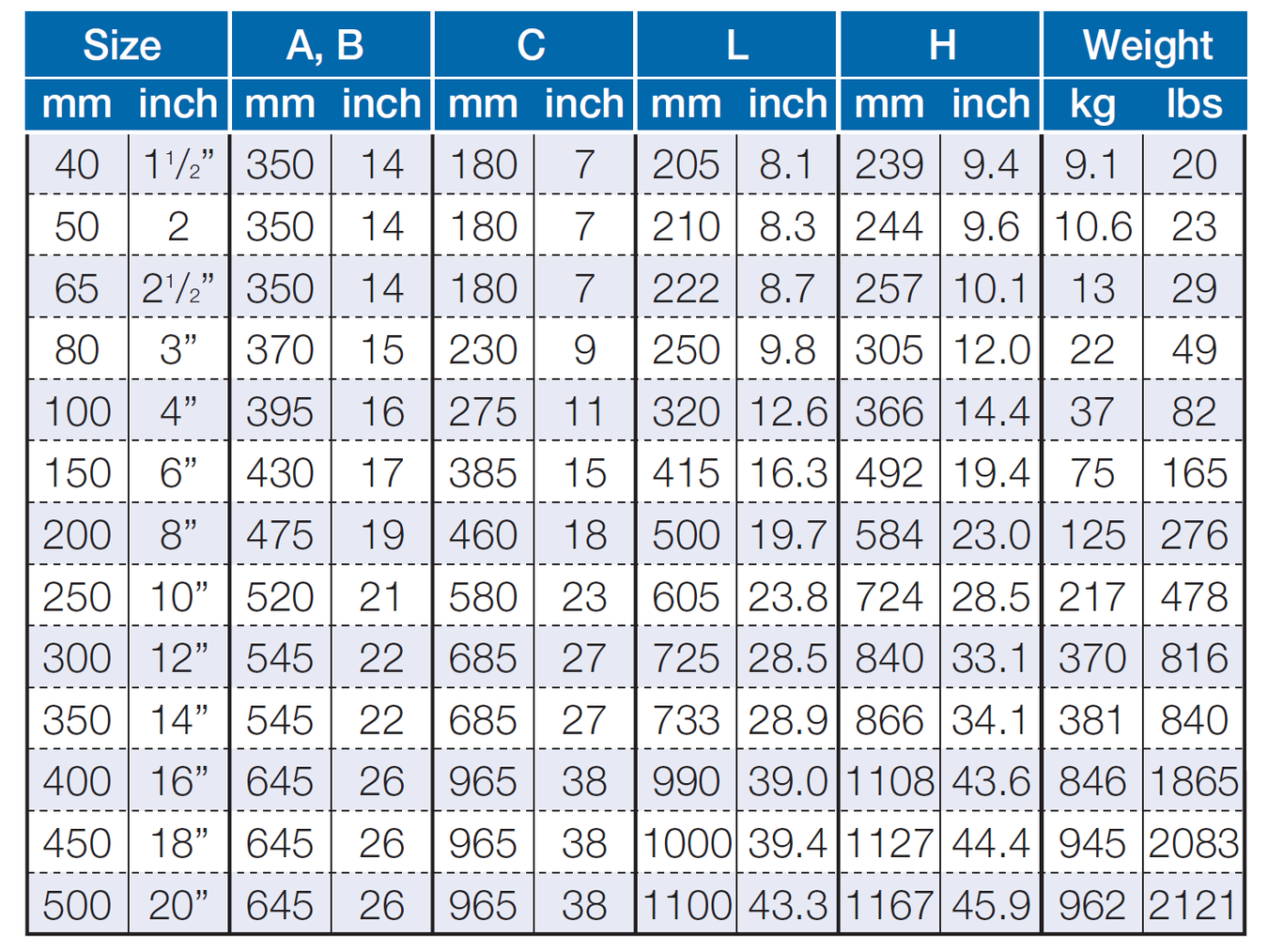
Data is for Y-pattern, flanged, PN16 valves
Weight is for PN16 basic valves
“C” enables removing the actuator in one unit
“L”, ISO standard lengths available
For more dimensions and weights tables, Please consult Deeco.
Technical Specifications
For technical specifications (Flow charts, valve characteristics, dimensions, etc.) - Please refer to the Engineering Data:
Bermad - Model 700 - Sigma EN/ES - Engineering Data
For Spare Parts & Repair Kits - Please refer to the base model:
Due to the wide range of options available and criteria for correct model selection, pricing and configuration are available on application only.
Please consult with Deeco engineers for more information.
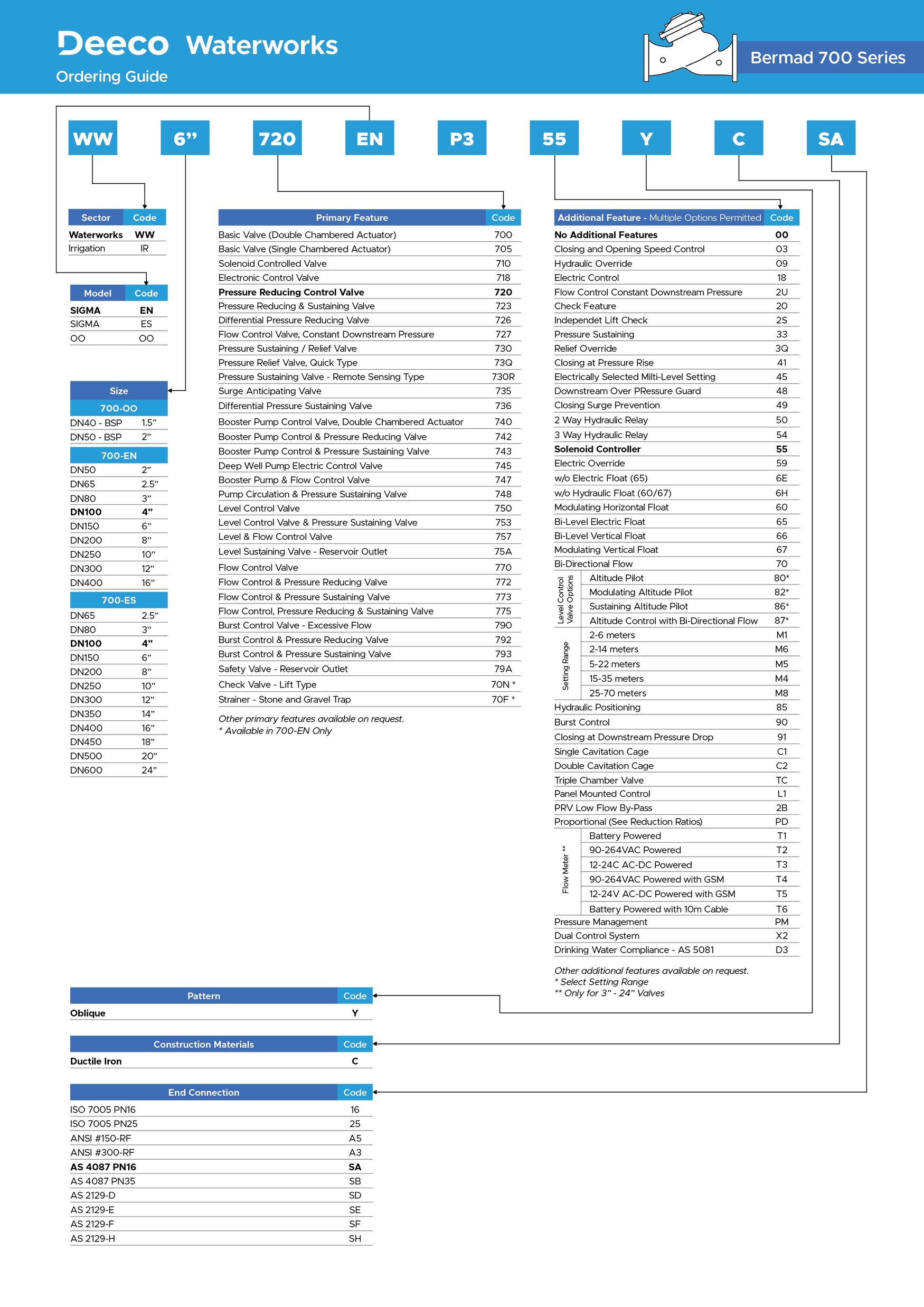
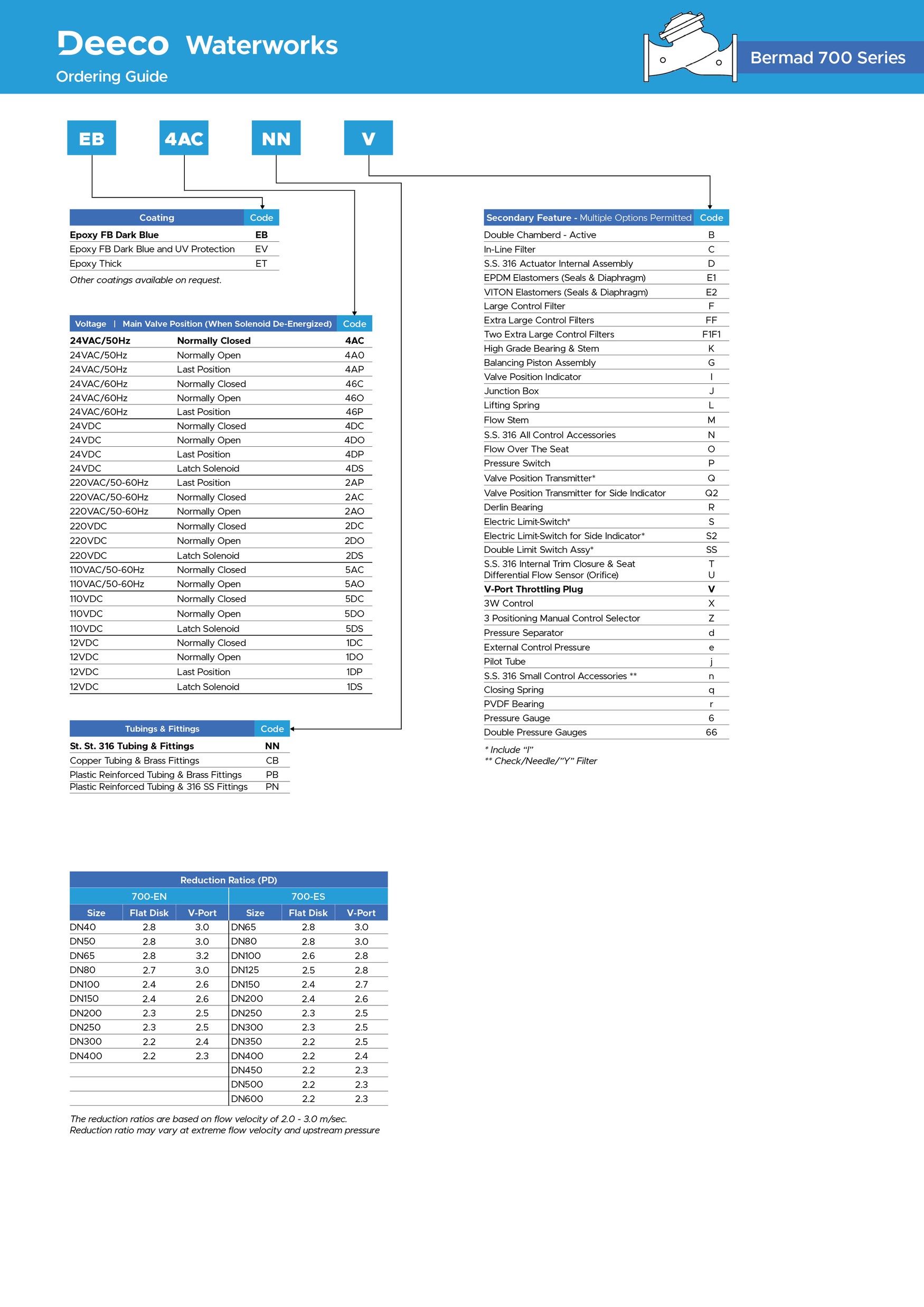